全员生产维修(TPM)是一种通过鼓励所有员工参与设备维护和改进,以实现设备可靠性最大化和生产效率提升的管理方法。
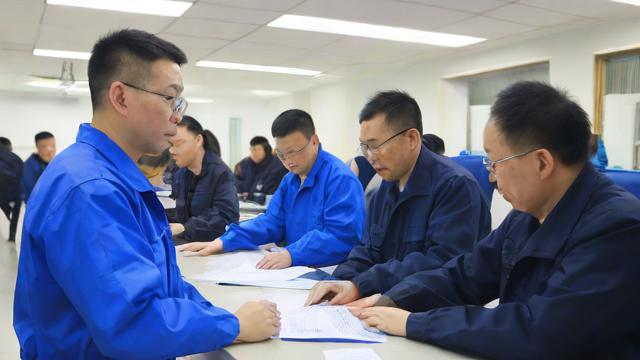
全员生产维修(Total Productive Maintenance,简称TPM)是一种综合性的设备管理和维护体系,旨在通过全员参与和预防性维护来提高设备的可靠性、减少故障停机时间,并最大化生产效率,以下是对全员生产维修的详细解释:
一、定义与目标
1、定义:全员生产维修是一种以设备综合效率最大化为目标,通过全系统的预防维修为过程,全体人员参与为基础的设备保养和维修管理体系,它强调从最高管理层到一线员工,每个人都参与到设备的维护和管理中来。
2、目标:
- 提高设备的综合效率(OEE),即设备的运行时间、性能效率和产品质量的综合体现。
- 实现“零”灾害、“零”不良、“零”浪费的目标,构建一个能够防止所有损失的体系。
- 通过持续改进和创新,不断提升企业的生产力和竞争力。
二、核心要素与特点
1、核心要素:
全效率:追求设备的经济性,使设备处于良好的技术状态,消除因突发故障引起的停机损失。
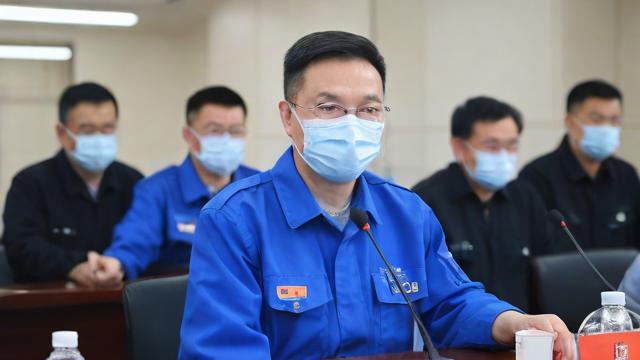
全系统:包括设备设计制造阶段的维修预防、设备投入使用后的预防维修和改善维修,对设备的一生进行全过程管理。
全员参与:不仅涉及设备管理和维修部门,还涉及计划、使用等所有部门,从企业领导到一线职工全体都要参加。
2、特点:
预防性维护:在设备出现故障之前,通过定期检查和保养找出潜在的问题,并进行修复和改进。
全员参与:鼓励所有员工参与到设备维护和改进中来,形成一种自主维修的文化。
持续改进:通过不断的评估和反馈,持续改进设备的性能和效率。
三、实施步骤与策略
1、准备阶段:
- 引进TPM计划,创造适宜的环境和氛围。
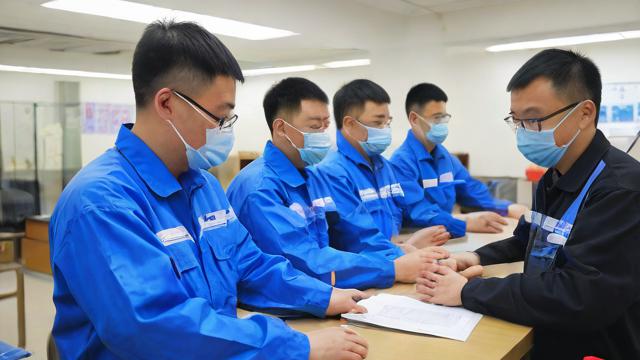
- 进行领导和员工的宣传培训,确保大家对TPM有清晰的认识和理解。
2、开始阶段:
- 举行TPM活动的开始仪式,正式宣布TPM活动的启动。
3、实施推进阶段:
- 制定具体的TPM活动计划,包括目标设定、责任分配、时间表等。
- 开展自主维修活动,鼓励员工对自己的设备进行日常维护和保养。
- 建立预防性维护体系,定期对设备进行检查和维护。
4、巩固阶段:
- 对TPM活动进行归纳和评估,识别存在的问题和不足。
- 根据评估结果,制定新的改进计划和目标,持续推动TPM活动的深入发展。
四、案例分析
某制造企业通过实施TPM项目,成功地将设备故障率降低了30%,生产效率提高了20%,具体措施包括:
- 成立专门的TPM推进小组,负责项目的策划和实施。
- 对所有员工进行TPM理念和技能的培训。
- 制定详细的TPM活动计划,包括日常维护、定期检查、故障处理等。
- 建立激励机制,对在TPM活动中表现突出的员工给予奖励。
五、常见问题解答
问:TPM与预防性维护有什么区别?
答:TPM是一种更全面的设备管理理念,它不仅包括预防性维护(在设备出现故障之前进行维护),还强调全员参与、自主维修和持续改进,预防性维护只是TPM的一个组成部分。
问:实施TPM需要多长时间才能看到效果?
答:实施TPM的时间因企业规模、设备状况和员工参与度等因素而异,企业在实施TPM几个月到一年内就能看到明显的效果,如设备故障率降低、生产效率提高等,但需要注意的是,TPM是一个持续改进的过程,需要长期坚持才能取得最佳效果。
六、小编有话说
全员生产维修(TPM)是一种先进的设备管理理念和方法,它强调全员参与、预防性维护和持续改进,通过实施TPM项目,企业可以显著提高设备的可靠性和生产效率,降低成本并提升竞争力,实施TPM也需要企业付出一定的努力和资源投入,包括建立专门的推进机构、进行员工培训、制定详细的活动计划等,企业在决定实施TPM时应充分考虑自身的实际情况和需求,并做好充分的准备和规划工作。